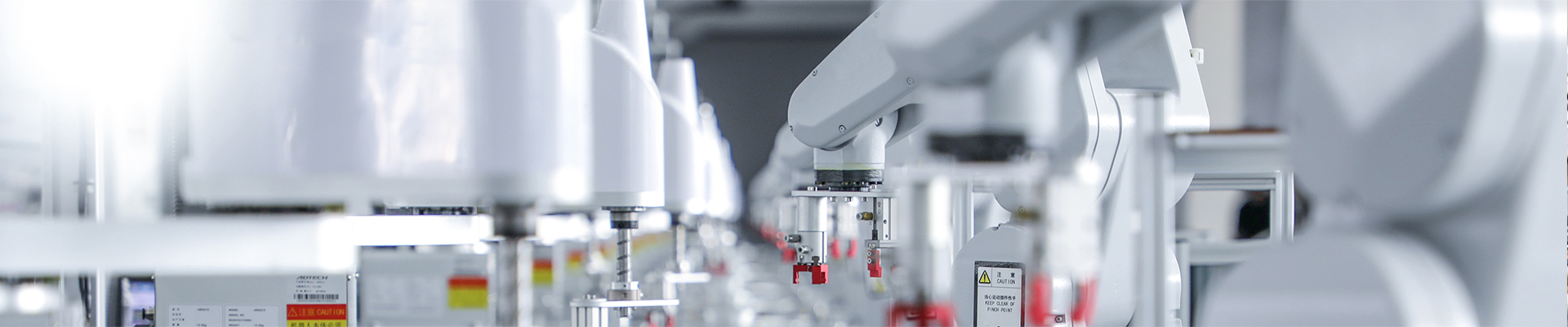
Cooling Tower FRP Structure
2020-04-14 11:02Fiber reinforced plastic (FRP), also known as fiber reinforced polymer, is in fact a composite material constituting a polymer matrix blended with certain reinforcing materials, such as fibers. The fibers are generally basalt, carbon, glass or aramid; in certain cases asbestos, wood or paper can also be used.
Most of these plastics are formed through various molding processes wherein a mold or a tool is used to place the fiber pre-form, constituting dry fiber or fiber containing a specific proportion of resin. After ‘wetting’ dry fibers with resin, “curing” takes place, wherein the fibers and matrix assume the mold’s shape. In this stage, there is occasional application of heat and pressure. The different methods include compression molding, bladder molding, mandrel wrapping, autoclave, filament winding, and wet layup, amongst others.
Pultruded glass fiber reinforced structural shapes and plates have a number of significant advantages over timber in many structural applications. Pultruded fiberglass will not rot or decay and is not susceptible to insect attack. Unlike wood, fiberglass requires no environmentally unfriendly preservatives or repellants, does not absorb any significant amount of water and is consistent in strength and appearance piece-to-piece (no culling). Pultruded fiberglass is stronger, more rigid and lighter weight than structural timber.
The other exclusive properties of fiber reinforced plastics include commendable thermal insulation, structural integrity, and fire hardness along with UV radiation stability and resistance to chemicals and other corrosive materials.
The characteristics of fiber reinforced plastics are dependent upon certain factors like mechanical properties of the matrix and fiber, the relative volume of both these components, and the length of the fiber and orientation within the matrix.
Any needs,please contact us.
Tianjin Latino Environmental Technology Co.,Ltd