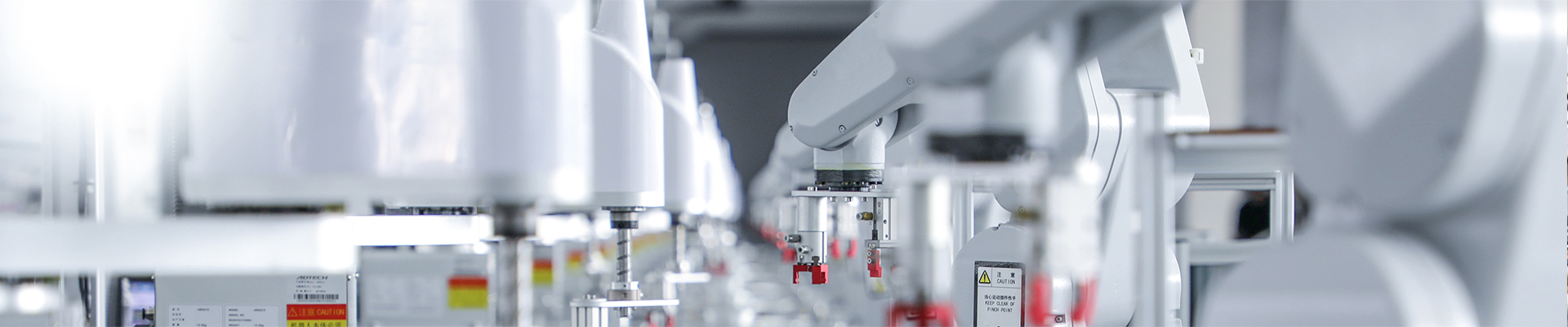
What is the role of packing in cooling towers?
2022-06-17 10:36The cooling tower packing is an important part of the cooling tower, and it also determines the working efficiency of the cooling tower. In essence, the filler is made of a PVC material. This material adopts the honeycomb design principle, which can improve the cooling power of the cooling tower when the cooling tower is working, greatly reduce the input consumption of the cooling tower, and increase the cooling capacity at the same time. cooling efficiency of the tower. The filler has a temperature resistance of 50°C to 68°C, aging resistance, excellent performance, UV resistance and long service life.
The function of the filler in the cooling tower is to increase the heat dissipation, prolong the residence time of the cooling water, increase the heat exchange area, and increase the heat exchange. Evenly distribute the water. Not stuffing something into a tower that needs to be cooled. A cooling tower is a device that cools hot fluids (including water) to a reasonable temperature. The waste heat generated in industrial production or refrigeration process is generally conducted away with cooling water. The function of the cooling tower is to exchange the cooling water with the waste heat with the air in the tower, so that the waste heat is transferred to the air and dissipated into the atmosphere. Application scope of cooling tower: air conditioning cooling system, refrigeration series, electric furnace, injection molding, tanning, power generation, steam turbine, aluminum profile processing, air compressor, industrial water cooling and other fields.
Cooling tower packing can be divided into: S wave packing, oblique staggered packing, stepped trapezoidal oblique wave packing, differential sine wave packing, point wave packing, hexagonal honeycomb packing, bidirectional wave packing, oblique wave packing, etc.
The materials used in cooling tower fillers are Xiaoshu, asbestos cement, cement grids, plastics, glass fiber reinforced plastics, ceramics, etc.
The earliest cooling towers used only wood. Due to the availability of wood, from the advent of cooling towers until the 1960s, the fill in cooling towers was almost exclusively made of wood.
Mahogany was the most commonly used material for early cooling tower fill due to its anti-corrosion properties. Mahogany that grows for a long time is straight and strong in shape, has a long service life, and is easy to use, so it is more expensive. Later, there was a shortage of old rosewood, and prices continued to climb.
In the 1950s and 1960s, asbestos cement sheet was widely used as a material for cooling tower fillers. This material has good corrosion resistance. However, it has been found that asbestos cement is harmful to the environment during processing and production, so the application of this material has gradually decreased, and some countries have banned it.
Around the 1970s, the emergence of plastic fillers was a major innovation in the development of cooling towers. Plastic fillers were first used in the heating ventilation and air conditioning industry, and later in the refining and power plant industries. This filler is characterized by good corrosion resistance and can be used for a long time. Plastic film packing is a major innovation in the history of cooling tower development.
It increases the contact area between water and air. Thereby having better cooling capacity. However, under the high temperature and humid working conditions of the cooling tower, the plastic filler will age and deform after working for about 3 years, which will affect the cooling efficiency. Moreover, freezing in winter will also have a greater impact on plastic fillers.
In recent years, ceramic fillers have gradually been used in cooling towers of power plants, and the characteristics of ceramic fillers are anti-aging. Geometric deformation is not easy to occur, no brittle crack, and anti-corrosion, good acid and alkali resistance. Another feature of this filler is that it has very good freeze resistance, and the service life of the ceramic filler is relatively long, and the service life is designed for 30 years. The initial investment of this kind of packing is relatively large, the unit does not need to replace the packing after 30 years of service, and the operation and maintenance cost is also lower than other materials.