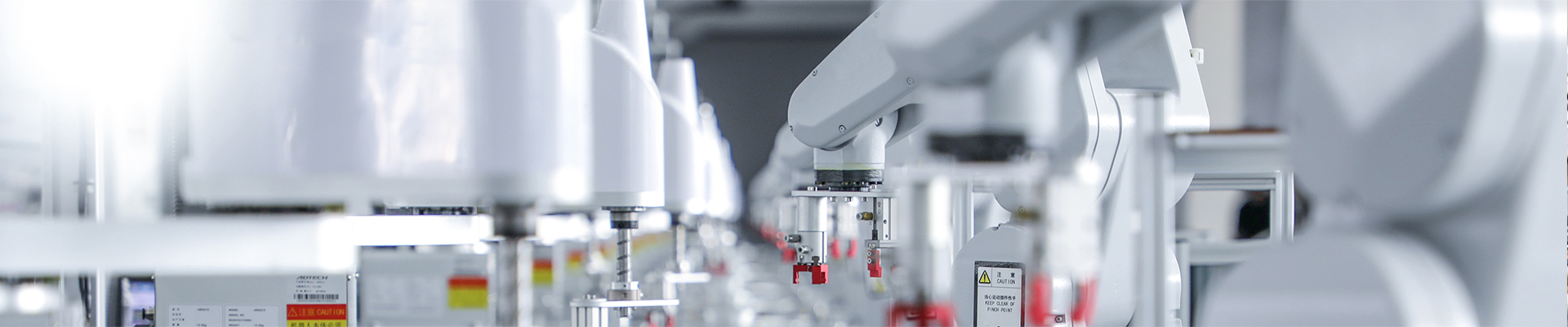
Reduce Maintenance and Boost Performance By Cooling Tower Life Hacks
2021-01-04 14:11Frankly speaking, cooling tower maintenance is very important for the usage of the cooling towers. That’s why most of the customers are always looking for answers on the follows:
1) How to reduce cooling tower maintenance (frequency, time, and hassle),
2) How to increase cooling tower performance.
The truth is, you can’t escape the cooling tower maintenance because by the cooling tower maintenance you could improve the cooling tower performance.
However, there are some “cooling tower life hacks” which will help you maintain your cooling tower operating at the original design level with little or no effort from you.
These solutions suitable for all kinds of cooling towers, and they offer the best cost-benefit out there. All these are inexpensive, but it have a significant impact in your cooling tower performance, and take a lot of cooling tower maintenance time off your plate.
Want more?
Let’s talk about the specific advantages of each of them.
Cooling Tower Air Inlet Louver
Have you ever asked yourself how is it possible that your cooling tower fill gets dirty so easily? The answer is through the air inlet entrance of your cooling tower, which is a big open door for whatever is in the air to come in.
As air comes into the tower, debris such as pollen, cottonwood, dust, and insects are also carried into your unit.
Problems caused by this are:
Clogged fill
Reduced airflow
Less cooling capability
Increased energy consumption
… and even debris reaching your chiller coils and affecting pump strainers if the situation persists.
To avoid having to deal with all this stress, facility teams spend hours manually cleaning the air inlets louver. Once cleaned, they suck even more debris into the cooling tower, and you get hooked in a frustrating situation in which the more you clean, the more you need to clean.
Thankfully a genius mind came up with an easy and cheap solution for the problem.
They are called air inlet screens. Custom-made to fit your unit perfectly, these screens prevent debris from coming into your tower in the first place, serving as a filter that only allows air to enter the unit.
They are strong, they last long, and they can be washed. Cleaning is as easy as dirt being swept off with a broom!
Imagine reducing maintenance time and effort by 70% and saving thousands of dollars a year. Sounds like magic, right?
These screens don’t shed fibers, don’t absorb moisture, and are installed with magnets for easy removal.
2. Sweeper System
Let’s talk about your cooling tower collection basin. You can basically compare it to a big bucket that collects sediments at the bottom of your tower, creating the perfect conditions for biological growth and a potential legionella outbreak.
It is vital to keep a clean system. Regular maintenance avoids problems related to water treatment, and also related to the structure of your unit, such as oxidation and rust.
A basin sweeper piping system is a simple supplemental filtration solution to prevent sediment from collecting in the cold-water basin and to save you maintenance costs.
It consists of a series of pipes and nozzles that use pressurized streams of water to direct sediment to the drain connection that sends the water to the filtration system. As a bonus, the constant turbulence inhibits biological growth.
Here are the main benefits of installing a sweeper piping system:
No built-up sediments
Less maintenance costs
Controlled biological growth
Integrates with your current water filtration system
Regular basin maintenance is recommended every 4 months, and it takes approximately 4 hours to be completed. The sweeper piping system can reduce up to 75% maintenance time and increase water treatment effectiveness by up to 10%.
Believe it or not, it only costs about $ 1,500 to install a sweeper piping system, with a payback period of a little over a year. If it sounds amazing, it’s because it is.
3. VFD Motor Packages
Not so long ago a VFD was considered a cooling tower upgrade alternative, but more and more environmental responsibility is turning it into a necessity. But why do YOU need one in your cooling tower?
That’s simple.
VFDs on cooling tower motors can significantly reduce energy costs compared to single or two-speed starters because it modulates fan speed and horsepower.
The tower operating costs can be lowered as much as 30% when compared to a two-speed motor system, and up to 70% compared to a single-speed motor system.
Also, VFDs maintain a tighter cold-water set-point temperature control than thermostats, which helps minimize your process cost.
And that goes without counting the state and utility rebates you can receive in California, that in some cases can reach 50% of the drive cost as energy savings incentive.
Sum up the total cost, energy savings, and rebates and we’re talking about a record payback: less than 2 years.
4. Water Level Controller
Have you ever thought of never having to replace float switches again? Liquid level controllers automatically control the water level in cooling towers, remote sumps, evaporative condensers, and closed-circuit fluid coolers.
These controllers use a microprocessor that monitors all sensor probes for correct operation and provides the corresponding outputs to drive the power relays, the BAS, and an indication of the operational status through led lights.
When compared to float switches, liquid level controllers win by far. They never foul, plate, or degrade, and they allow for much better water level management.
The package usually comes with the water level control sensor, the mounting assembly for the sensor, and the control panel.
The most common application for a water level control system is water makeup. When the water level drops below a preset level, a solenoid valve will fill the basin again to the proper level.
In addition, liquid level control systems accomplish these functions:
Low water alarm
Low water cutoff
High water alarm
High water cutoff
They warn you about abnormal operating levels and protect pumps from operating with insufficient water, even turning it off to prevent costly repairs.
5. Extended Lubrication Lines
Extended lubrication lines with grease fittings can be used to lubricate fan shaft bearings or to oil gearboxes without any hassle.
These components require quarterly lubrication, and to pump grease directly into them successfully, you need to be able to easily access them in the tower, which is not guaranteed.
So why not make life easier and have extended grease lines that run outside the cooling tower casing panel, with a grease zerk located outside the tower?
Not only do they facilitate year-round maintenance, but they also increase equipment reliability.
In case you decide to use extended lube lines, just make sure that the grease lines are not damaged, and the fittings are still intact. Otherwise, the lube will be dripping into your cooling tower instead of lubricating the parts.
Want to boost your cooling tower performance and have less work to do every day starting now? Then give us a call!
Factory Authorized Service is the only company you’ll need to plan a proper maintenance plan for your cooling tower—and the rest of your industrial HVAC system. We have experience in servicing all the major brands, including Evapco, Baltimore Aircoil, Marley, Recold, and more! Contact us today to start the process of ensuring your cooling tower is reliable, safe, and performing at optimum energy efficiency.